Introduction
In this post we’ll discuss PVC plastic packaging, how it is manufactured and it’s uses but most importantly, how it is recycled. Polyvinyl, also known as poly(vinyl chloride) or PVC, is the third most widely produced synthetic plastic. There are three forms of PVC; rigid, flexible and liquid. The rigid and flexible variants are by far the most common form, having various applications in a number of industries. Rigid PVC is most commonly used in the irrigation and construction sectors, whereas flexible PVC is widely used in the medical and clothing industries.
PVC can be recycled multiple times and each year 730,000 tonnes of PVC are recycled around the world. It is a very versatile and cost-efficient thermoplastic of good dimensional stability and impact strength (when plasticized), and excellent weathering properties. It can be easily extruded, calendared and die-cut, and is printable with conventional screen and offset printing methods. Depending on the composition, it can be clear or matt, coloured or white, and rigid or flexible. It can also be easily reprocessed using heat
What is PVC?
Plastics, or synthetic resins, are classified into two broad categories: thermosetting resins and thermoplastic resins. PVC falls into the thermoplastic resins, which also include polyethylene (PE), polystyrene (PS) and polypropylene (PP). These hard plastics can be softened again through heating. On the other hand, thermosetting resins, that include phenolic resin and melamine resin, are thermally hardened and never become soft again. PVC has a rather polar backbone with strong intermolecular interactions. It is, therefore, rigid at room temperature. However, it can be easily softened (plasticized) by blending with plasticizer during fabrication. This versatility is a major advantage of vinyl polymers.
PVC film is used as shrink and stretch wrap for industrial and consumer goods and as pallet wrap, however, on a much smaller scale than polyolefin films. Other uses include bags, liners, bottle sleeving, adhesive tape backing, labels, blood bags and I.V. bags. It is often PVDC coated when improved moisture barrier properties are required.
FDA approved PVC is a good choice to package fresh red meat because it is semi-permeable, meaning, it is just enough oxygen permeable to keep meat products fresh and to maintain its bright red color. When transparency is important, PVC is often used. It is naturally white and very brittle (before the additions of plasticizers) plastic. It is a thermoplastic material, which means that it can be reprocessed using heat.
PVC has been around longer than most plastics, first synthesized in 1872 and commercially produced by B.F. Goodrich Company in the 1920s. By comparison, many other common plastics were first synthesized and commercially viable only in the 1940s and 1950s. It is used most commonly in the construction industry and is also used for signs, healthcare applications, and fiber for clothing. PVC was accidentally discovered twice, once in 1832 by French chemist Henri Victor Regnault, and then rediscovered in 1872 by a German man named Eugene Baumann.
The first patent for a polymerisation process to manufacture PVC was granted to German inventor Friedrich Klatte in 1913 and PVC has been in commercial production since 1933. The material now accounts for about 20% of all plastic manufactured world-wide, second only to polyethlene.
PVC film without plasticizer is called rigid vinyl film, whereas plasticized PVC is called flexible vinyl film
Flexible Vinyl Film
Flexible vinyl film has good barrier properties to oil and grease but is oxygen permeable. It also has good cling, excellent clarity and puncture resistant. These properties make flexible PVC suitable for food packaging to keep meat and other perishable produce fresh (when FDA approved). However, plasticized PVC has a lower melting point, is less resistant to chemicals, and has a lower ultimate tensile strength than rigid vinyl. Flexible PVC is used to produce drip bags, electrical insulation, vehicle dashboard skins, gumboots, safety gloves, garden hoses and packaging films.
Rigid Vinyl Film
Rigid vinyl, also known as unplasticized polyvinyl chloride (uPVC), is a strong and lightweight film. It is one of the most durable low-cost films and is resistant to many chemicals. Generally, uPVC can be used at temperatures up to 60°C. It has higher tensile strength and modulus than flexible PVC, but has low impact toughness, and is subject to stress cracking depending on the environment.
PVC has several limitations and drawbacks; the plasticizer can harden in cold conditions and soften under hot conditions, which lead to a change in properties and can compromise the strength of the seal. PVC also releases small amounts of hydrogen chloride into the air and produces carbon deposit onto the sealing equipment when heated. For this reason, good ventilation is required when sealing PVC shrink-wrap. Its characteristics such as clarity, formability at lower temperatures, easy printability make it a product of convenience. Rigid PVC is used to manufacture irrigation pipes, conduit, gutters, pharmaceutical bottles, and fridge magnets.
How PVC Plastic is made?
The essential raw materials for PVC are derived from salt and oil. The electrolysis of salt water produces chlorine, which is combined with ethylene (obtained from oil or gas) to form vinyl chloride monomer (VCM). Molecules of VCM are polymerised to form PVC resin, to which appropriate additives are incorporated to make a customised PVC compound.
The PVC production process consists of 5 steps:
- The extraction of salt and hydrocarbon resources
- The production of ethylene and chlorine from these resources
- The combination of chlorine and ethylene to make the vinyl chloride monomer (VCM)
- The polymerisation of VCM to make poly-vinyl-chloride (PVC)
- The blending of PVC polymer with other materials to produce different formulations providing a wide range of physical properties.
PVC production uses less unrenewable resources / fossil fuel – oil or natural gas – than other plastics, and it can therefore be regarded as a resource-saving plastic. In contrast, the production of plastics such as PE, PP, PET and PS is completely dependent on oil or gas.
PVC is manufactured from two starting materials;
- 57% of the molecular weight derived from common salt
- 43% derived from hyrdocarbon feedstocks (increasingly ethylene from sugar crops is also being used for PVC production as an alternative to ethylene from oil or natural gas)
Whilst PVC is most frequently made from salt and oil, in some regions of the world PVC is made without using oil feedstock at all (substituting oil-derived hydrocarbon with bio-derived hydrocarbon feedstock). PVC is therefore far less oil-dependent than other thermoplastics. It is also highly durable and energy efficient across a range of applications, which makes for an extremely effective use of raw materials.
There are over 50 quadrillion tonnes of salt exist dissolved in the sea, with over 200billion tonnes of salt available underground – reserves of this material are clearly abundant
Ethylene from oil equates to 0.3% of annual oil usage, but increasingly etheylene from sugar crops is also being used for PVC production
Physical Properties
Although plastics seem very similar in the context of daily use, PVC has completely different features in terms of performance and functions compared with other plastics.
Some of the most significant properties of Polyvinyl Chloride (PVC) are:
- Density: PVC is very dense compared to most plastics (specific gravity around 1.4)
- Economics: PVC is readily available and cheap.
- Hardness: Rigid PVC ranks well for hardness and durability.
- Strength: Rigid PVC has excellent tensile strength.
Benefits of PVC Plastic
- PVC has excellent electrical insulation properties, making it ideal for cabling applications. Its good impact strength and weatherproof attributes make it ideal for construction products.
- PVC has extensive European food contact and medical approvals
- PVC is easy to process, long lasting, tough and light
- PVC consumes less primary energy during production than any of the other commodity plastics
- With high clarity and excellent organoleptic properties (no transfer of taint to food) it is equally suited for use in short term applications such as specialised packaging.
- PVC has a relatively small carbon footprint, the below infographic indicates the CO2 impact PVC compared to other products
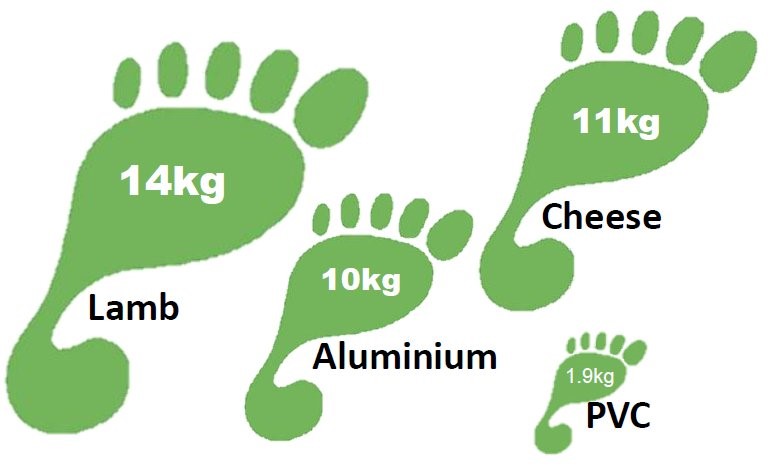
- PVC windows help to cut energy bills and PVC-based windows account for most BFRC ‘A’ Rated Energy Efficient Windows
- PVC is fully recyclable. Due to its properties it reprocesses well and can be recycled into second (or third life) applications with ease.
- PVC has numerous unique characteristics that make it a valuable packaging and plastic material. It is highly resistant to environmental degradation, including wear and tear, chemicals and alkaline substances. It is cheap to produce and requires little energy in the process, making it an economically-beneficial polymer.
- PVC has a high density and good tensile strength, especially the rigid form. This makes it a popular polymer for the construction and irrigation sectors, where the plastic needs to be able to withstand impacts and hard use. Its high resistance to chemicals and heat also makes it a valuable polymer. PVC is inherently flame-resistant and impermeable to liquids.
- All PVC pipes manufactured in South Africa have been lead-free since 2006 after local manufacturers belonging to the Southern African Plastic Pipe Manufacturers Association (SAPPMA) voluntarily, but at great cost to the industry, accepted a policy of heavy metal-free stabilizers for the manufacture of PVC pipes based on health and environmental considerations.
- As a member of the Southern African Vinyls Association (SAVA), SAPPMA is also one of the signatories of the Association’s Product Stewardship Commitment (PSC) a voluntary programme aimed at ensuring that all heavy metal additives (primarily lead) are removed from their workplace environments
- These characteristics of PVC make it a versatile and highly useful plastic material. It is easy to recycle and is readily available, making it a valuable polymer for the recycling industry. All PVC plastic should be reused, upcycled or sent to a recycling facility when no longer needed. It should never be sent to landfills or dumped in the environment.
What are the Advantages of Polyvinyl Chloride?
PVC provides industries with a series of critical advantages that have cemented its place as one of the most popular and widely used plastics on the market. These advantages include:
- Polyvinyl Chloride is readily available and relatively inexpensive.
- Polyvinyl Chloride is very dense and thus very hard and resists impact deformation very well relative to other plastics.
- Polyvinyl Chloride has outstanding tensile strength.
- Polyvinyl Chloride is very resistant to chemicals and alkalis.
PVC’s advantages helped solidify its place as one of the most used plastics around the world. However, even though it’s widely effective and popular, you have to consider some factors when using the material.
What are the Disadvantages of Polyvinyl Chloride?
While PVC has a host of advantages that make it a desirable material to work with, there are some reasons to take caution. The disadvantages that you have to account for when using PVC include:
- Polyvinyl Chloride has very poor heat stability. For this reason, additives that stabilize the material at higher temperatures are typically added to the material during production.
- Polyvinyl Chloride emits toxic fumes when melted or subject to a fire.
Although there are some shortcomings, Polyvinyl Chloride is an excellent material overall. It has a unique blend of qualities that make it particularly useful for the construction business. By taking note and accounting for the shortcomings of the material, you can effectively navigate and compensate so you can effectively use the material in your upcoming projects.
Recycling of PVC
PVC can be easily identified by its recycling code #3.
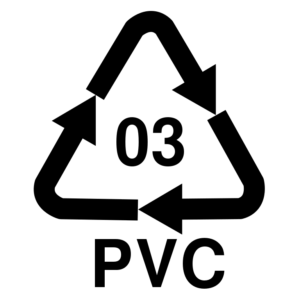
The environmental impacts of any one material cannot be judged in isolation since the use of alternatives will not be without cost, either financially or to the environment. Materials that compete with PVC are often promoted as a more natural choice, indeed, ‘natural’ does not equate to ‘better’ or ‘more sustainable’.
Some competing materials claim environmental and sustainability advantages over PVC – this is usually based either on myths about the environmental impact of PVC or unjustifiably biased opinions about the competing materials.
The structure and composition of PVC lends itself to being mechanically recycled, with reasonable ease, to produce good quality recycling material. As with most recycling streams, sorting is of the utmost importance to achieve optimal recycling of PVC materials.
Across the world, the PVC industry has invested heavily to develop sophisticated recycling schemes to ensure that large amounts of PVC can be reused in a new generation of advanced energy efficient, sustainable products.
South Africa has some of the highest recycling rates in the world – just under 21 000 tonnes of PVC plastic was recycled in 2018 alone. Of this volume, most of the PVC plastic came from gumboots, cables, hosepipes, plumbing pipes, conduit and gutters. These materials are mainly recycled into shoe soles, car mats and plastic speed humps.
PVC recyclate is currently in high demand due to its various applications and low energy requirements. This plastic is inherently flame-resistant and is impermeable to liquids. PVC is cost-effective to manufacture and, because of its versatility, it is an abundant plastic polymer. It is widely used in the construction, irrigation, medical, mining and motoring industry as a result of these properties.
PVC can also be recycled into various rigid, flexible and liquid products, including rubber shoes, flooring, trays, mats, insulation, raincoats and many more. The clothing and footwear industry purchases the majority portion of PVC recyclate, followed by the construction and agriculture sectors. This polymer has many uses as a recycled material in various industries in South Africa.
Processing PVC plastics requires special machinery. Many small-scale recyclers in South Africa cannot process PVC.
There are two ways to recycle PVC; mechanical recycling by grinding it into small pellets which are then melted and remoulded into new products, or feedstock recycling where chemical processes break down the polymer into its basic chemical components. Both of these methods are used in South Africa but the mechanical recycling method is more common.
Unlike feedstock (chemical) recycling, mechanical recycling keeps the original composition of the PVC waste. This poses a problem because many PVC products contain additives and additional chemicals to make them rigid or flexible. For example, flexible PVC contains added plasticizers to increase the fluidity of the product.
Even products used for similar applications may contain different amounts of additives, which makes mechanical recycling more difficult. PVC recyclate requires very specific compositions for different applications. In order to produce a high-quality recyclate, the PVC waste should be separated into uniform compositions before being mechanically processed.
This is where feedstock recycling has its advantages. By breaking down the recyclate into its basic chemical components, a mix of unsorted PVC products can be processed at the same time. However, feedstock recycling is more expensive than mechanical processing and the end-market for the recovered chemicals is not as big. This gives recyclers fewer incentives to use chemical methods to process PVC waste.
The PVC waste that comes from post-consumer sources is often mixed in type and quality. On the other hand, PVC waste from post-industrial sources (factories) is often the same. This means that it is far easier to mechanically recycle the waste from post-industrial sources as it does not need to be sorted first. Post-consumer sources of waste require careful separation before being mechanically processed.
Post-industrial waste is relatively pure as it comes straight from the factories that produce one type of product (or products with similar chemical compositions). This waste is easy to collect and recycle since it comes directly from the source or the manufacturer and the quality is high. Post-consumer waste contains mixed materials that were used for various applications and the quality of the waste is often degraded.
In Closing
Plastics are often perceived as symbols of throwaway or single use. However, in reality plastics are durable materials that do not rust or corrode. PVC is an exceptionally durable plastic: the majority of PVC applications have a service life of between 10 and 100 years, and more than half these will last for over 15 years. The strength of this polymer lends itself to a lifetime of reuse, making PVC a valuable plastic. By reusing and recycling these products, we can maximise their usefulness while minimising their environmental impact.
PVC is a popular plastic material because of its advantageous properties. During the manufacturing process, chlorine is obtained from ordinary salt and is chemically combined with ethylene, which is derived from coal in South Africa. PVC is always compounded with additives to give it a range of properties, such as rigidity, flexibility, fire resistance and liquidity.
PVC has excellent resistance to wear and tear, making it ideal for products that need to withstand hard usage over many years. It is lightweight, cost-effective and requires little energy to manufacture. PVC is highly valuable in this regard as it supports economic development and the environment, unlike many plastic alternatives. These properties make PVC a popular plastic polymer. It is widely recycled in South Africa thanks to our strong and resilient recycling industry.
All materials, and PVC is no exception, have sustainability issues. These arise from their specific properties but also from the ways in which they are used throughout their life cycle, and the ways in which they are disposed of.
Where PVC differs from other materials is in the PVC industry’s understanding of its sustainability, which is perhaps better than many manufacturers of other synthetic materials. What’s more, the PVC industry is working systematically to address PVC’s sustainability challenges, so as to ensure its useful role in a more sustainable future for mankind.
At Waxpak, we Manufacture and Distribute food grade plastic packaging, mostly in rPET, High impact polysyrene and Polyprop, but our sister company Dispak Industries produces various PVC sheeting and packaging solutions to meet whatever your need may be.
Everything we manufacture is 100% recyclable and we welcome drop off’s at our facility in Chamdor, Krugersdorp. With a reputation for stringent quality to exacting standards, we hold A BRC Global Standard for Packaging and Packaging Materials.
[mailpoet_form id=”1″]
“Polyvinyl Films”, https://polymerdatabase.com/Films/PVC.html
“All About Plastics: What is PVC?”, January 11, 2021, https://www.plasticsinfo.co.za/2021/01/11/all-about-plastics-what-is-pvc/
“How PVC packaging is recycled in South Africa”, November 20, 2019, https://www.plasticsinfo.co.za/2019/11/20/how-pvc-packaging-is-recycled-in-south-africa/
“PVC plastic success in South Africa”, November 20, 2019, https://www.plasticsinfo.co.za/2019/11/20/pvc-plastic-successes-in-south-africa/
“PVC – a circular material for the future”, https://pvc.org/
“Polycinyl Chloride PVC”, https://www.bpf.co.uk/plastipedia/polymers/pvc.aspx
“Everything You Need To Know About PVC Plastic”, July 6, 2016 https://www.creativemechanisms.com/blog/everything-you-need-to-know-about-pvc-plastic
WWF Plastics report: 02 November 2020, https://wwfafrica.awsassets.panda.org/downloads/wwf_plastics_report_final_2nov2020.pdf